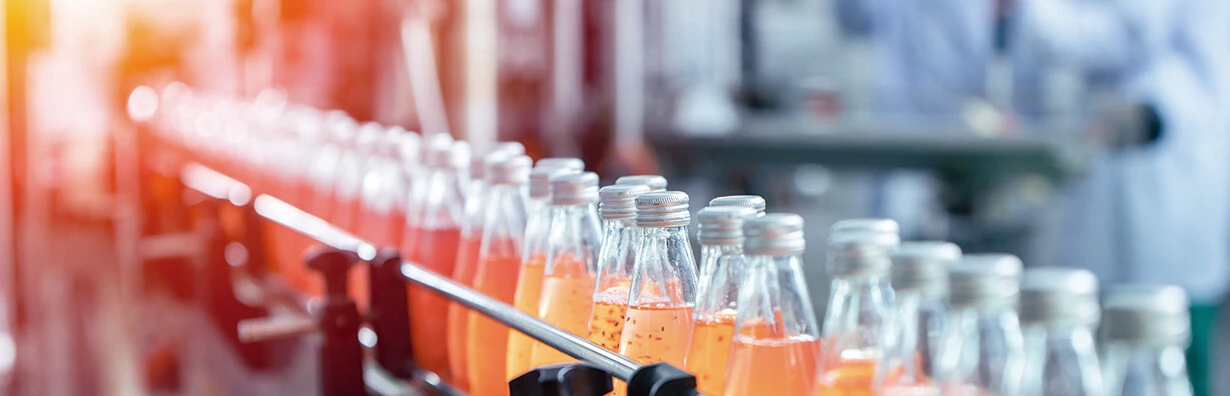
26.06.2025
Cómo reducir el tiempo de inactividad de la producción de su empresa
¿Hay una baja de producción? Solo si es una estrategia de la empresa, como cuando es necesario realizar mantenimiento predictivo o reemplazar maquinaria con equipos que aumenten la productividad. De lo contrario, es una señal de que se avecinan pérdidas. El tiempo de inactividad puede volverse peligroso si no se planifica, y es por esta y otras razones que la reducción del tiempo de inactividad de la producción es una prioridad para la mayoría de los gerentes. A continuación, enumeramos las principales razones que causan tiempos de inactividad no programados y cómo reducir el tiempo de inactividad de su producción.
Las causas más comunes de paradas de producción no programadas
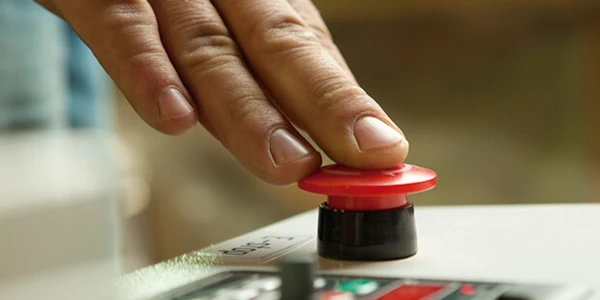
En primer lugar, es necesario comprender las razones de una parada de producción para crear estrategias que las reduzcan. Existen muchos factores que provocan tiempos de inactividad, como:
- Error operativo.
- Mantenimiento mínimo del equipo.
- Equipos averiados.
- Falta de materias primas.
- Accidentes laborales.
Uno de los escenarios más temidos en una fábrica es cuando un área se detiene y, como resultado, se produce un efecto dominó en otros sectores que esperan la finalización de procesos anteriores para entregarles piezas.
Cuanto más tiempo se tarde en completar los procesos y terminar un producto, mayor será el coste de comercializarlo.
Por eso, es importante centrarse en reducir el tiempo que los empleados o las máquinas permanecen inactivos para aumentar la eficiencia de los resultados de su sector.
7 consejos para reducir el tiempo de inactividad de la producción en su industria
1. Invertir en la comunicación del equipo
La comunicación entre gerentes y empleados es esencial para mejorar la eficiencia en todos los departamentos. Para que un empleado se sienta parte del equipo, el supervisor debe explicar la relación entre el tiempo de inactividad y su impacto en los resultados del negocio. Esta participación hace que el empleado se sienta parte de decisiones importantes y estrategias operativas. Mantener a los empleados comprometidos es esencial para aumentar la productividad, especialmente porque los miembros del equipo felices y motivados contribuyen mejor al objetivo final de reducir el tiempo de inactividad.
2. Evaluar al equipo periódicamente
La mayoría de las empresas realizan evaluaciones de desempeño periódicas, pero puede enriquecer su retroalimentación incluyendo un análisis del tiempo de inactividad. Estas evaluaciones deben ser honestas y directas, y centrarse en lo que la gerencia considera áreas de excelencia y áreas de mejora. Con la retroalimentación adecuada, los empleados se mantendrán motivados para ayudar a reducir el tiempo de inactividad.
3. Establecer objetivos específicos
Establezca objetivos de incentivos diarios, trimestrales y semestrales para reducir errores y mejorar la productividad. Incorpore la escucha activa en esta estrategia: escuchar las sugerencias de los trabajadores de la línea de producción los integra en el proceso de toma de decisiones. Capacitar a los operadores sobre cada parte del proceso de fabricación puede ayudarles a comprender mejor su función y trabajo específicos. Al garantizar que todos los empleados tengan incentivos para destacar y considerar sus sugerencias, los gerentes se ven recompensados con una mayor productividad.
4. Realizar un mantenimiento periódico de los activos.
Una de las razones más comunes de las paradas no programadas es descuidar la necesidad de realizar mantenimiento predictivo a los equipos. Las empresas que monitorean, inspeccionan, actualizan y reparan sus máquinas tienen menos probabilidades de sufrir interrupciones de producción y de personal en momentos inoportunos. Además, evitan sorpresas desagradables cuando las máquinas se averían sin previo aviso. Incluya un plan de mantenimiento regular para mantener las máquinas funcionando al máximo rendimiento durante el mayor tiempo posible. De esta manera, incluso si es necesario detener la producción para reemplazar piezas o cambiar el aceite, por ejemplo, este tiempo de ajuste dentro de la planificación siempre será menor que el de una parada inesperada.
5. Utilice dispositivos y software de monitorización
¿Cómo sabe cuándo detenerse para realizar mantenimiento predictivo o preventivo? Mediante el uso constante de dispositivos y software para monitorear sus máquinas principales. Son esenciales para identificar las primeras señales de falla. Los sensores inteligentes pueden recopilar datos de vibración e identificar posibles problemas que podrían causar fallas en los equipos. Invierta en esta tecnología para optimizar la reducción del tiempo de inactividad en su industria.
6. Mantener existencias de materia prima.
Las paradas imprevistas también pueden deberse a la falta de materias primas. Entre las razones comunes de la falta de materiales en el inventario que se deben abordar se incluyen:
- Cambios inesperados en la demanda de los clientes.
- Problemas en la cadena de suministro.
- Promesas incumplidas a los clientes.
- Supervisión inadecuada de los plazos de entrega.
- Niveles de inventario insuficientes.
- Vencimiento del inventario.
7. Sea estricto en el cumplimiento de las normas de seguridad.
Por último, pero no menos importante, asegúrese de que todos los empleados cumplan con las normas de seguridad para las actividades que realizan. Además de estar al día con la legislación, esta medida previene accidentes laborales que podrían comprometer la salud y la seguridad de los trabajadores y, en consecuencia, causar paradas de producción no programadas. ¿Listo para poner en práctica todos estos consejos y reducir las paradas de producción en su sector? ¡Manos a la obra!